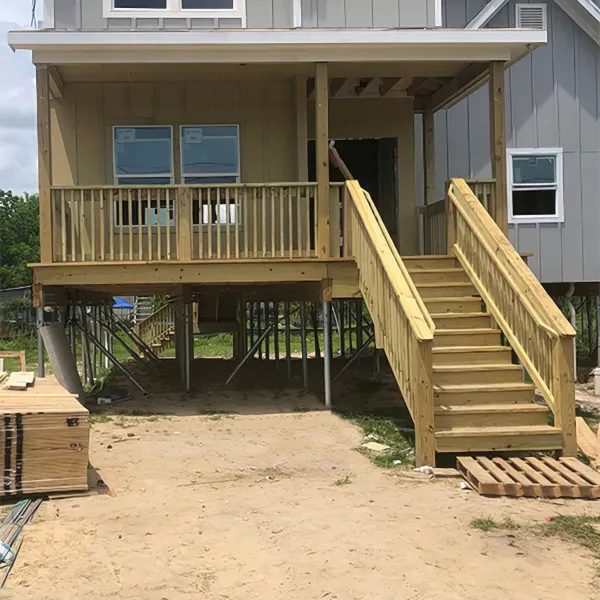
Case Study
Crosby, TX - Two Story Post-Hurricane Home Elevation
Situation
In the aftermath of Hurricane Harvey, a devastating natural disaster that
unleashed a record-breaking 60.58 inches of rainfall in 2017, the suburban
Houston community faced a daunting challenge. This property suffered extensive flood damage, and rebuilding was awarded through the Harris
County (TX) Hurricane Recovery Program. This community, like others in the
region, had to retool its flood zones and building codes in the wake of this
devastation. Traditionally, the go-to approach would involve shallow
foundations supported by piers or columns to elevate structures above
floodwaters. This approach, however, creates the likelihood of future structural
damage from soil expansive heave and shrinkage. A challenge arose to find a
sustainable and competitively priced long-term foundation system that could
not only withstand future floods but also meet the evolving standards and
regulations set forth by the county.
Scope of Work
The primary objective of this project was to devise a robust foundation design
capable of elevating a two-story structure above the newly established flood
elevation levels mandated in the aftermath of Hurricane Harvey. This
elevation was imperative not only to safeguard the property against future flood damage but also to counteract the threat of soil expansion, which can
cause an uplift to the structure. Cost-effectiveness was a top consideration as
well. Helical piles are a proven solution, striking a balance between resiliency
and affordability. Cobalt Engineering designed the 2078 square-foot home
above the new flood elevation. Many battered piles were incorporated into
the design, due to the additional lateral loading on the structure.
Anchor System
86 total. 64 vertical and 22 battered piles installed. 2-7/8" OD pipe piles with single 12" and single 14" helix were used. Single helix opted over multi-helix due to the presence of expansive clay soils, preventing the need to advance the piles deeper to ensure all helices are past the active soil. The foundation design required a minimum of 5 Kips for compression load and 2.5 Kips for tension load on the battered piles. While these loads may appear light in nature for a two-story structure, the spacing was kept to a minimum to allow for additional piles to increase the overall lateral capacity.
Result
Cantsink helical piles proved to be an exceptional choice for this project. The entire pile installation process was completed within three days, allowing the framer to proceed with no downtime. The piles reached a minimum embedment of 13', surpassing the 10' active zone requirement. Additionally, the minimum torque achieved for each pile exceeded 2,000 foot-pounds, which translates to an ultimate load more than three times what is required. The project was completed within the proposed budget, demonstrating that Cantsink helical piles not only deliver superior performance but also offer a cost-effective elevation support solution for both one- and two-story structures.
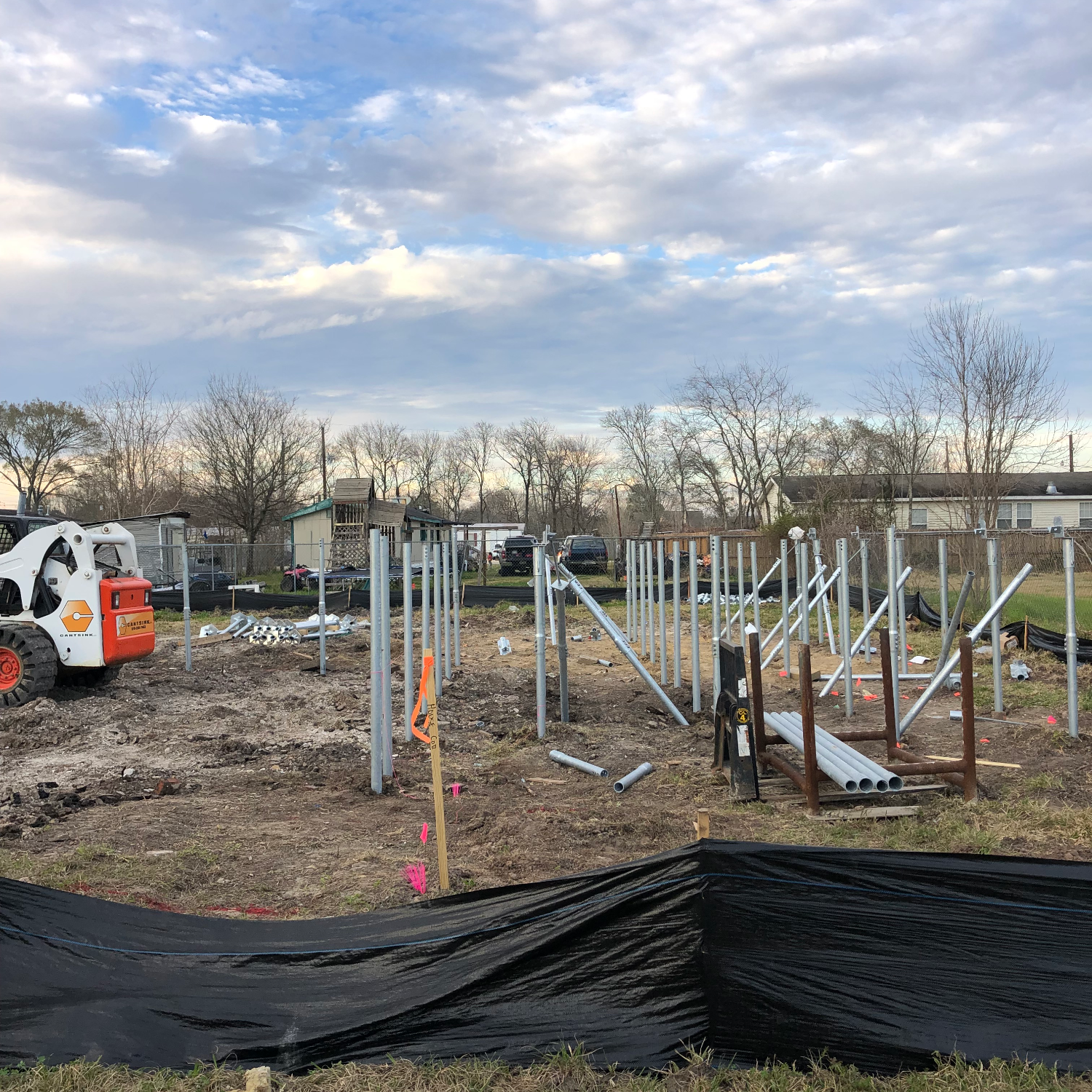
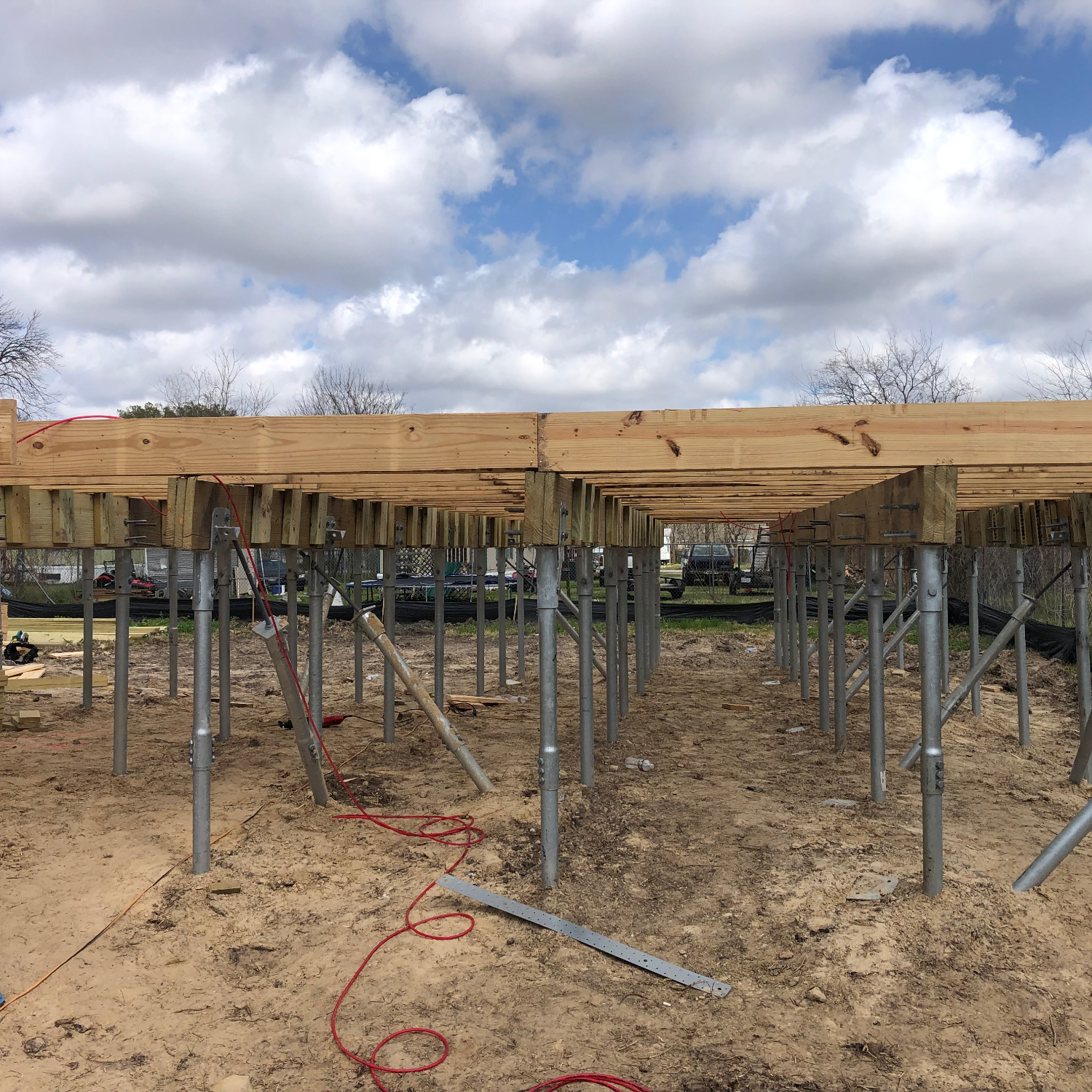
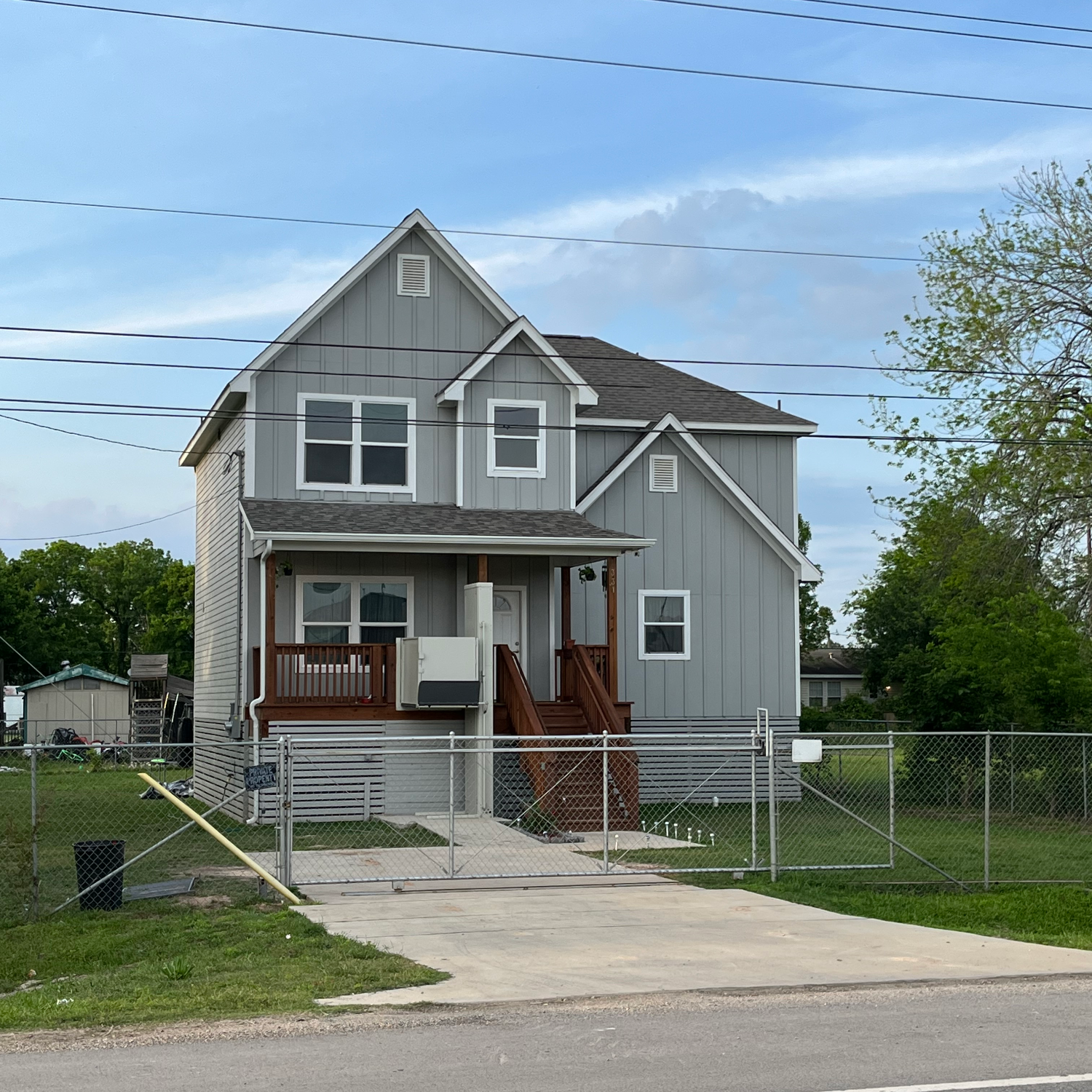